Destylator przemysłowy to urządzenie, które służy do oddzielania składników mieszanin cieczy na podstawie różnicy w ich temperaturach wrzenia. Proces ten jest kluczowy w wielu branżach, takich jak chemia, petrochemia czy produkcja alkoholu. W destylacji wykorzystuje się zjawisko parowania i skraplania, co pozwala na uzyskanie czystych substancji. W praktyce, destylatory przemysłowe mogą mieć różne formy i rozmiary, od małych jednostek laboratoryjnych po ogromne kolumny destylacyjne stosowane w rafineriach. Zasadniczo proces rozpoczyna się od podgrzewania cieczy, co prowadzi do jej parowania. Para następnie przemieszcza się w górę kolumny, gdzie schładza się i skrapla, a uzyskany produkt zbiera się w odpowiednich zbiornikach. Kluczowym elementem efektywności destylatora jest jego konstrukcja oraz zastosowane materiały, które muszą wytrzymać wysokie temperatury i ciśnienia.
Jakie są rodzaje destylatorów przemysłowych i ich zastosowanie
W przemyśle istnieje wiele rodzajów destylatorów, które różnią się zarówno konstrukcją, jak i zastosowaniem. Najpopularniejsze z nich to destylatory prostoliniowe oraz kolumnowe. Destylatory prostoliniowe są najczęściej używane do prostych procesów separacji, gdzie nie ma potrzeby uzyskania bardzo czystych frakcji. Z kolei destylatory kolumnowe są bardziej zaawansowane technologicznie i pozwalają na wielokrotne oddzielanie składników, co jest niezbędne w przypadku produkcji wysokiej jakości substancji chemicznych czy alkoholi. Inne typy to destylatory frakcyjne, które umożliwiają separację wielu składników jednocześnie oraz destylatory próżniowe, które działają w obniżonym ciśnieniu, co pozwala na destylację substancji o wysokich temperaturach wrzenia bez ich degradacji. Każdy z tych typów ma swoje specyficzne zastosowanie w różnych gałęziach przemysłu, od farmaceutycznego po spożywczy.
Jakie są kluczowe elementy budowy destylatora przemysłowego
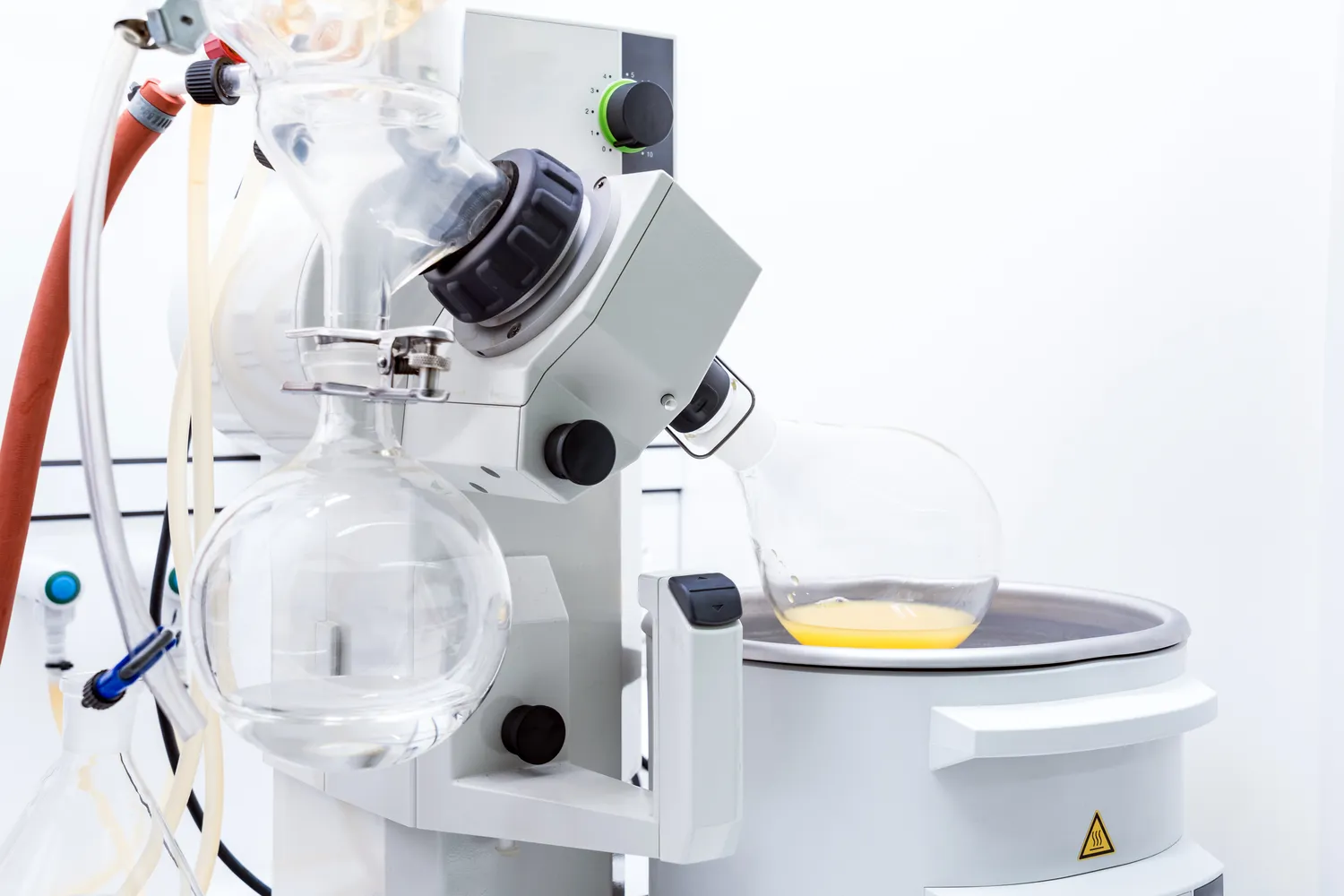
Budowa destylatora przemysłowego opiera się na kilku kluczowych elementach, które mają istotny wpływ na jego funkcjonowanie oraz efektywność procesu destylacji. Podstawowym elementem jest zbiornik do podgrzewania cieczy, który musi być wykonany z materiałów odpornych na wysokie temperatury oraz korozję. Kolejnym istotnym komponentem jest kolumna destylacyjna, która pełni rolę miejsca separacji pary od cieczy. Wewnątrz kolumny znajdują się różnego rodzaju elementy takie jak półki czy packingi, które zwiększają powierzchnię kontaktu między parą a cieczą, co sprzyja lepszemu oddzieleniu składników. Ważnym elementem jest również kondensator, który schładza parę i przekształca ją z powrotem w ciecz. Oprócz tych podstawowych części, nowoczesne destylatory często wyposażone są w systemy automatyzacji oraz monitoringu, co pozwala na precyzyjne kontrolowanie parametrów procesu oraz zwiększa bezpieczeństwo pracy.
Jakie są korzyści z używania nowoczesnych destylatorów przemysłowych
Nowoczesne destylatory przemysłowe oferują szereg korzyści, które przekładają się na efektywność produkcji oraz jakość uzyskiwanych produktów. Przede wszystkim dzięki zastosowaniu zaawansowanych technologii możliwe jest osiągnięcie wyższej wydajności procesu destylacji przy jednoczesnym zmniejszeniu zużycia energii. Nowoczesne urządzenia często wyposażone są w systemy recyklingu ciepła oraz automatyczne sterowanie procesem, co pozwala na optymalizację warunków pracy i minimalizację strat surowców. Kolejną zaletą jest możliwość uzyskania produktów o bardzo wysokiej czystości chemicznej, co jest szczególnie istotne w branżach takich jak farmaceutyka czy chemia specjalistyczna. Dodatkowo nowoczesne destylatory charakteryzują się większą niezawodnością oraz mniejszymi wymaganiami konserwacyjnymi dzięki zastosowaniu materiałów odpornych na korozję oraz innowacyjnych rozwiązań konstrukcyjnych.
Jakie są najczęstsze problemy z destylatorami przemysłowymi
Destylatory przemysłowe, mimo zaawansowanej technologii, mogą napotykać różnorodne problemy, które wpływają na ich wydajność oraz jakość uzyskiwanych produktów. Jednym z najczęstszych problemów jest zatykanie kolumny destylacyjnej, co może prowadzić do obniżenia efektywności separacji. Zatykanie to może być spowodowane osadzaniem się zanieczyszczeń lub niepożądanych substancji, co wymaga regularnych przeglądów i czyszczenia. Innym istotnym problemem jest niewłaściwe ustawienie parametrów procesu, takich jak temperatura czy ciśnienie, co może prowadzić do nieefektywnej destylacji i obniżonej jakości produktu końcowego. W przypadku destylatorów próżniowych, niewłaściwe utrzymanie próżni może skutkować niepożądanym wrzeniem cieczy i utratą składników lotnych. Dodatkowo, awarie systemów automatyzacji mogą prowadzić do nieprzewidzianych przestojów w produkcji. W związku z tym kluczowe jest regularne monitorowanie stanu technicznego destylatorów oraz przeprowadzanie konserwacji zgodnie z zaleceniami producenta.
Jakie są koszty zakupu i eksploatacji destylatora przemysłowego
Koszty zakupu oraz eksploatacji destylatora przemysłowego mogą się znacznie różnić w zależności od jego typu, wielkości oraz zastosowania. Przy zakupie należy uwzględnić nie tylko cenę samego urządzenia, ale także koszty instalacji oraz ewentualnych modyfikacji infrastruktury zakładu. Nowoczesne destylatory często wymagają zaawansowanych systemów chłodzenia oraz dostępu do mediów energetycznych, co może zwiększać początkowe wydatki. Koszty eksploatacji obejmują zużycie energii, konserwację oraz ewentualne naprawy. Warto zauważyć, że nowoczesne destylatory, dzięki swojej efektywności energetycznej, mogą w dłuższej perspektywie przyczynić się do obniżenia kosztów operacyjnych. Dodatkowo, regularne przeglądy techniczne oraz odpowiednia konserwacja mogą pomóc w uniknięciu kosztownych awarii i przestojów w produkcji. W przypadku dużych zakładów przemysłowych warto również rozważyć opcje leasingu lub wynajmu urządzeń, co może być korzystną alternatywą dla zakupu na własność.
Jakie są innowacje technologiczne w dziedzinie destylatorów przemysłowych
W ostatnich latach obserwuje się dynamiczny rozwój technologii związanych z destylacją przemysłową, co znacząco wpływa na efektywność procesów produkcyjnych. Innowacje te obejmują zarówno nowe materiały konstrukcyjne, jak i zaawansowane systemy automatyzacji. Przykładem są kolumny destylacyjne wykonane z materiałów kompozytowych, które charakteryzują się wysoką odpornością na korozję oraz lepszym przewodnictwem cieplnym. Dzięki temu możliwe jest osiągnięcie wyższej efektywności separacji przy niższym zużyciu energii. Kolejnym istotnym kierunkiem rozwoju są systemy monitoringu oparte na sztucznej inteligencji, które umożliwiają bieżące śledzenie parametrów pracy destylatora oraz prognozowanie potencjalnych awarii. Dzięki tym rozwiązaniom można szybko reagować na zmiany w procesie i optymalizować jego przebieg. Innowacyjne technologie pozwalają także na integrację procesów destylacyjnych z innymi etapami produkcji, co sprzyja zwiększeniu efektywności całego zakładu.
Jakie są wymagania dotyczące bezpieczeństwa w pracy z destylatorami przemysłowymi
Bezpieczeństwo pracy z destylatorami przemysłowymi jest kluczowym aspektem każdej działalności produkcyjnej związanej z tymi urządzeniami. Pracownicy muszą być odpowiednio przeszkoleni w zakresie obsługi urządzeń oraz znajomości procedur bezpieczeństwa. Niezbędne jest stosowanie odpowiednich środków ochrony osobistej, takich jak okulary ochronne, rękawice czy odzież robocza odporna na działanie chemikaliów. Ważnym elementem jest również zapewnienie odpowiedniej wentylacji w pomieszczeniach, gdzie znajdują się destylatory, aby uniknąć gromadzenia się szkodliwych oparów czy gazów. Regularne przeglądy techniczne urządzeń są niezbędne do wykrywania potencjalnych usterek i zapobiegania awariom, które mogłyby prowadzić do zagrożeń dla zdrowia pracowników lub środowiska. Dodatkowo przedsiębiorstwa powinny wdrażać procedury awaryjne na wypadek wystąpienia incydentów związanych z pracą destylatorów, takie jak wycieki substancji chemicznych czy pożary.
Jakie są przyszłe kierunki rozwoju technologii destylacyjnej
Przyszłość technologii destylacyjnej wydaje się obiecująca dzięki ciągłemu postępowi naukowemu i technologicznemu. Jednym z głównych kierunków rozwoju jest dalsza automatyzacja procesów produkcyjnych poprzez zastosowanie sztucznej inteligencji i uczenia maszynowego do optymalizacji parametrów pracy destylatorów. Dzięki temu możliwe będzie szybsze dostosowywanie warunków pracy do zmieniających się potrzeb produkcyjnych oraz minimalizacja strat surowców i energii. Ponadto rośnie zainteresowanie ekologicznymi rozwiązaniami technologicznymi, takimi jak wykorzystanie energii odnawialnej czy recykling ciepła odpadowego w procesach destylacyjnych. W miarę wzrostu świadomości ekologicznej przedsiębiorstw można spodziewać się większego nacisku na rozwój technologii przyjaznych dla środowiska oraz redukcję emisji gazów cieplarnianych związanych z procesami przemysłowymi. Również rozwój materiałów o lepszych właściwościach mechanicznych i chemicznych pozwoli na budowę bardziej wydajnych i trwałych urządzeń destylacyjnych.
Jakie są kluczowe czynniki wpływające na wybór destylatora przemysłowego
Wybór odpowiedniego destylatora przemysłowego to złożony proces, który zależy od wielu czynników. Przede wszystkim należy uwzględnić rodzaj substancji, które mają być destylowane, ponieważ różne składniki chemiczne mogą wymagać różnych metod separacji. Ważnym aspektem jest również wydajność urządzenia oraz jego zdolność do pracy w określonych warunkach temperaturowych i ciśnieniowych. Koszty zakupu i eksploatacji stanowią kolejny istotny element decyzji, dlatego warto przeprowadzić dokładną analizę ekonomiczną. Dodatkowo, dostępność serwisu technicznego oraz wsparcia producenta mogą mieć duże znaczenie dla długoterminowej efektywności działania destylatora. Warto również zwrócić uwagę na innowacyjność technologii oraz możliwość integracji z istniejącymi systemami produkcyjnymi.