Budowa maszyn pneumatycznych opiera się na kilku kluczowych elementach, które współdziałają ze sobą w celu efektywnego wykorzystania energii sprężonego powietrza. Podstawowym komponentem jest sprężarka, która odpowiada za wytwarzanie sprężonego powietrza. Sprężarki mogą być różnego rodzaju, w tym tłokowe, śrubowe czy wirnikowe, a ich wybór zależy od wymagań dotyczących ciśnienia i wydajności. Kolejnym istotnym elementem są zbiorniki ciśnieniowe, które przechowują sprężone powietrze i umożliwiają jego dalsze wykorzystanie w systemie. W układzie pneumatycznym niezbędne są także zawory sterujące, które regulują przepływ powietrza oraz kierunek jego ruchu, co pozwala na precyzyjne sterowanie pracą maszyny. Warto również wspomnieć o siłownikach pneumatycznych, które przekształcają energię sprężonego powietrza w ruch mechaniczny. Siłowniki te mogą mieć różne kształty i rozmiary, co pozwala na ich zastosowanie w różnych aplikacjach przemysłowych.
Jakie są zalety i wady maszyn pneumatycznych
Maszyny pneumatyczne cieszą się dużą popularnością w różnych branżach przemysłowych ze względu na swoje liczne zalety. Przede wszystkim charakteryzują się one prostotą konstrukcji oraz łatwością w obsłudze, co sprawia, że są idealnym rozwiązaniem dla wielu zastosowań. Dzięki wykorzystaniu sprężonego powietrza jako medium roboczego, maszyny te są bezpieczne w użyciu, ponieważ nie stwarzają ryzyka wybuchu ani pożaru. Ponadto, maszyny pneumatyczne są zazwyczaj lżejsze od ich elektrycznych odpowiedników, co ułatwia ich transport i instalację. Warto również zwrócić uwagę na ich elastyczność – można je łatwo dostosować do różnych zadań poprzez zmianę narzędzi roboczych lub konfiguracji układu. Niemniej jednak istnieją także pewne wady związane z użytkowaniem maszyn pneumatycznych. Jedną z nich jest konieczność posiadania źródła sprężonego powietrza oraz systemu rurociągów do jego dystrybucji, co może wiązać się z dodatkowymi kosztami instalacyjnymi.
Jakie zastosowania mają maszyny pneumatyczne w przemyśle
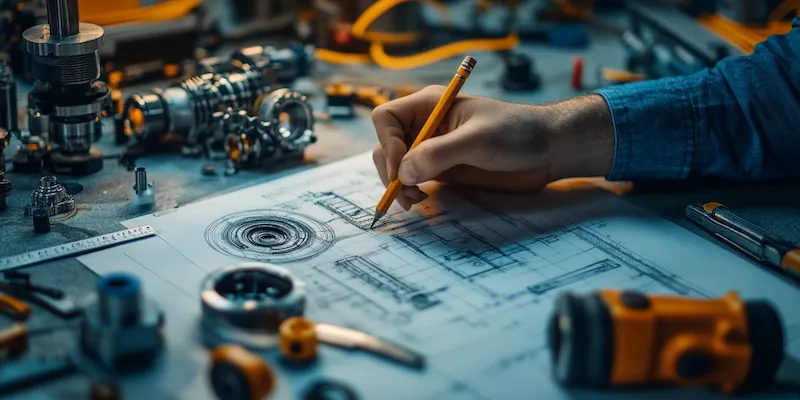
Maszyny pneumatyczne znajdują szerokie zastosowanie w różnych dziedzinach przemysłu dzięki swojej wszechstronności i efektywności. W branży produkcyjnej często wykorzystuje się je do automatyzacji procesów montażowych oraz pakowania produktów. Siłowniki pneumatyczne mogą być stosowane do podnoszenia ciężkich elementów lub precyzyjnego manipulowania nimi, co zwiększa wydajność pracy oraz redukuje ryzyko urazów pracowników. W przemyśle motoryzacyjnym maszyny pneumatyczne są wykorzystywane do malowania pojazdów oraz wykonywania różnych operacji montażowych, takich jak przykręcanie śrub czy łączenie elementów karoserii. Również w branży spożywczej maszyny te znajdują zastosowanie przy pakowaniu żywności oraz transportowaniu surowców. W obszarze budownictwa maszyny pneumatyczne są używane do wiercenia otworów oraz rozbiórek dzięki swojej dużej mocy i wydajności.
Jakie nowinki technologiczne dotyczą budowy maszyn pneumatycznych
W ostatnich latach obserwuje się dynamiczny rozwój technologii związanych z budową maszyn pneumatycznych, co wpływa na ich wydajność oraz funkcjonalność. Nowoczesne sprężarki wyposażane są w zaawansowane systemy sterowania elektronicznego, które pozwalają na optymalizację pracy urządzeń oraz zmniejszenie zużycia energii. Dzięki temu możliwe jest osiągnięcie lepszej efektywności energetycznej oraz redukcja kosztów eksploatacyjnych. Również materiały używane do produkcji elementów maszyn ulegają zmianom – coraz częściej stosuje się kompozyty oraz lekkie stopy metali, co przekłada się na zmniejszenie masy urządzeń i poprawę ich mobilności. Innowacyjne rozwiązania obejmują także rozwój inteligentnych systemów monitorowania stanu technicznego maszyn pneumatycznych, które umożliwiają przewidywanie awarii oraz planowanie konserwacji przed wystąpieniem problemów. Takie podejście pozwala na zwiększenie niezawodności urządzeń oraz minimalizację przestojów produkcyjnych.
Jakie są najczęstsze problemy związane z maszynami pneumatycznymi
Maszyny pneumatyczne, mimo swoich licznych zalet, mogą napotykać różne problemy, które wpływają na ich wydajność i niezawodność. Jednym z najczęściej występujących problemów jest nieszczelność w układzie pneumatycznym. Nieszczelności mogą prowadzić do utraty ciśnienia, co z kolei obniża efektywność pracy maszyny. Warto regularnie kontrolować wszystkie połączenia oraz uszczelki, aby zminimalizować ryzyko wystąpienia tego typu awarii. Kolejnym istotnym problemem jest zanieczyszczenie sprężonego powietrza, które może pochodzić z różnych źródeł, takich jak wilgoć czy cząstki stałe. Zanieczyszczone powietrze może powodować uszkodzenia elementów roboczych oraz obniżać wydajność maszyn. Dlatego tak ważne jest stosowanie odpowiednich filtrów oraz systemów osuszania powietrza. Inne problemy mogą dotyczyć niewłaściwego ustawienia parametrów pracy maszyn, takich jak ciśnienie czy prędkość działania siłowników. Niewłaściwe ustawienia mogą prowadzić do nadmiernego zużycia komponentów oraz obniżenia jakości wykonywanych operacji.
Jakie są różnice między maszynami pneumatycznymi a hydraulicznymi
Maszyny pneumatyczne i hydrauliczne to dwa różne typy urządzeń wykorzystywanych w przemyśle, które mają swoje unikalne cechy oraz zastosowania. Główna różnica między nimi polega na medium roboczym – maszyny pneumatyczne wykorzystują sprężone powietrze, podczas gdy maszyny hydrauliczne działają na zasadzie cieczy hydraulicznej. Dzięki temu maszyny pneumatyczne są lżejsze i łatwiejsze w obsłudze, co sprawia, że idealnie nadają się do zastosowań wymagających dużej mobilności oraz elastyczności. Z drugiej strony maszyny hydrauliczne charakteryzują się większą mocą i zdolnością do przenoszenia cięższych ładunków, co czyni je bardziej odpowiednimi do zastosowań przemysłowych wymagających dużej siły roboczej. W kontekście wydajności energetycznej warto zauważyć, że maszyny pneumatyczne mogą być mniej efektywne niż hydrauliczne w dłuższym okresie czasu, ponieważ sprężone powietrze łatwiej ucieka przez nieszczelności. Z drugiej strony maszyny hydrauliczne mogą wymagać bardziej skomplikowanej infrastruktury oraz systemu filtracji cieczy, co zwiększa koszty ich eksploatacji.
Jakie są koszty budowy i eksploatacji maszyn pneumatycznych
Koszty budowy i eksploatacji maszyn pneumatycznych mogą się znacznie różnić w zależności od wielu czynników, takich jak rodzaj zastosowania, skala produkcji oraz specyfika używanych komponentów. Na etapie budowy kluczowe znaczenie ma wybór odpowiednich elementów układu pneumatycznego, takich jak sprężarki, zbiorniki ciśnieniowe czy zawory sterujące. Koszt tych komponentów może się znacznie różnić w zależności od producenta oraz technologii wykonania. Dodatkowo należy uwzględnić koszty instalacji systemu rurociągów oraz ewentualnych systemów filtracji i osuszania powietrza. Warto również pamiętać o kosztach związanych z konserwacją i serwisowaniem maszyn, które są niezbędne dla zapewnienia ich prawidłowego funkcjonowania przez dłuższy czas. Regularne przeglądy techniczne oraz wymiana zużytych elementów mogą generować dodatkowe wydatki. Koszty eksploatacyjne związane z energią elektryczną potrzebną do pracy sprężarek również powinny być brane pod uwagę przy ocenie całkowitych kosztów użytkowania maszyn pneumatycznych.
Jakie są przyszłościowe kierunki rozwoju technologii pneumatycznych
Przyszłość technologii pneumatycznych zapowiada się obiecująco dzięki ciągłemu postępowi w dziedzinie automatyzacji oraz cyfryzacji procesów przemysłowych. Jednym z kluczowych kierunków rozwoju jest integracja maszyn pneumatycznych z systemami Internetu Rzeczy (IoT), co pozwoli na zbieranie danych o ich pracy w czasie rzeczywistym oraz analizowanie ich za pomocą zaawansowanych algorytmów analitycznych. Taki krok umożliwi lepsze monitorowanie stanu technicznego urządzeń oraz przewidywanie awarii zanim one nastąpią, co przyczyni się do zwiększenia niezawodności i efektywności produkcji. Kolejnym ważnym trendem jest rozwój materiałów kompozytowych i lekkich stopów metali, które pozwalają na budowę lżejszych i bardziej wytrzymałych komponentów maszyn pneumatycznych. Dzięki temu możliwe będzie osiągnięcie lepszej mobilności urządzeń oraz ich większej wydajności energetycznej. Również automatyzacja procesów montażowych i pakowania przy użyciu robotyki współpracującej z systemami pneumatycznymi staje się coraz bardziej popularna, co otwiera nowe możliwości dla przemysłu 4.0.
Jakie są kluczowe zasady bezpieczeństwa przy pracy z maszynami pneumatycznymi
Bezpieczeństwo pracy z maszynami pneumatycznymi jest niezwykle istotne ze względu na potencjalne zagrożenia związane z używaniem sprężonego powietrza jako medium roboczego. Kluczową zasadą jest regularne przeprowadzanie szkoleń dla pracowników dotyczących obsługi tych urządzeń oraz zasad bezpieczeństwa. Pracownicy powinni być świadomi ryzyka związanego z nieszczelnościami w układzie pneumatycznym oraz skutków niewłaściwego użytkowania sprzętu. Ważne jest także stosowanie odpowiednich środków ochrony osobistej, takich jak gogle ochronne czy rękawice, aby minimalizować ryzyko urazów podczas pracy z maszynami pneumatycznymi. Kolejnym istotnym aspektem jest regularna kontrola stanu technicznego urządzeń – wszelkie nieszczelności czy uszkodzenia powinny być natychmiast usuwane przez wykwalifikowany personel serwisowy. Należy również przestrzegać zasad dotyczących ciśnienia roboczego – przekroczenie dopuszczalnych wartości może prowadzić do niebezpiecznych sytuacji związanych z wybuchem lub uszkodzeniem sprzętu.