Destylacja rozpuszczalników to proces, który polega na oddzieleniu składników mieszaniny na podstawie różnicy w ich temperaturach wrzenia. Jest to jedna z najstarszych metod separacji substancji chemicznych, która znajduje zastosowanie w wielu dziedzinach, w tym w przemyśle chemicznym, farmaceutycznym oraz w laboratoriach. Proces ten rozpoczyna się od podgrzewania cieczy, co powoduje jej parowanie. W wyniku tego pary unoszą się do góry, a następnie skraplają się w chłodnej części aparatu destylacyjnego. Otrzymany kondensat jest zbierany jako destylat, który zawiera składniki o niższej temperaturze wrzenia. W przypadku rozpuszczalników, takich jak etanol czy aceton, destylacja pozwala na uzyskanie czystych substancji poprzez usunięcie zanieczyszczeń oraz innych składników o wyższej temperaturze wrzenia. Proces ten może być przeprowadzany w różnych warunkach ciśnienia, co wpływa na efektywność separacji oraz jakość otrzymanego produktu.
Jakie są rodzaje destylacji rozpuszczalników i ich zastosowania
W kontekście destylacji rozpuszczalników wyróżniamy kilka podstawowych rodzajów tej metody, które różnią się techniką oraz zastosowaniem. Najpopularniejszą formą jest destylacja prosta, która jest stosowana do oddzielania substancji o znacznie różniących się temperaturach wrzenia. Przykładem może być oddzielenie wody od alkoholu etylowego. Kolejnym rodzajem jest destylacja frakcyjna, która umożliwia separację składników o podobnych temperaturach wrzenia. Ten proces jest szczególnie przydatny w przemyśle petrochemicznym do uzyskiwania różnych frakcji ropy naftowej. Destylacja azeotropowa to kolejna technika, która polega na dodawaniu substancji pomocniczej w celu zmiany właściwości mieszaniny i ułatwienia separacji składników. Zastosowanie tej metody można zaobserwować w produkcji wysokopurego alkoholu czy estrów. Ostatnim rodzajem jest destylacja próżniowa, która odbywa się w obniżonym ciśnieniu i pozwala na destylację substancji termolabilnych, które mogłyby ulec rozkładowi w wyższych temperaturach.
Jakie są korzyści z wykorzystania destylacji rozpuszczalników
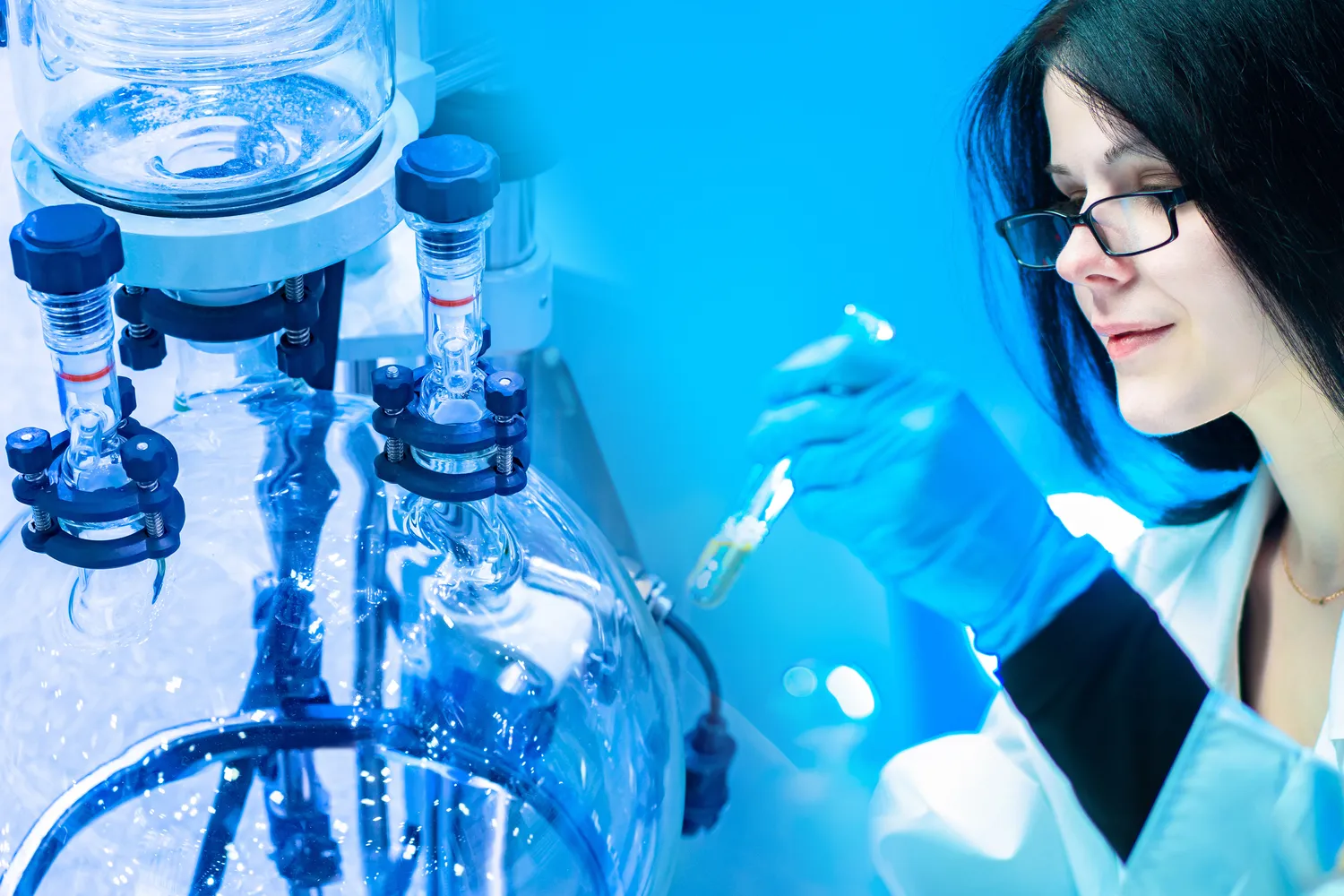
Wykorzystanie destylacji rozpuszczalników niesie ze sobą wiele korzyści zarówno dla przemysłu, jak i dla laboratoriów badawczych. Przede wszystkim proces ten pozwala na uzyskanie wysokiej czystości produktów chemicznych, co jest kluczowe w wielu zastosowaniach, zwłaszcza w farmacji i chemii analitycznej. Dzięki możliwości separacji składników o różnych temperaturach wrzenia można skutecznie eliminować zanieczyszczenia oraz niepożądane substancje z końcowego produktu. Ponadto destylacja jest procesem relatywnie prostym i łatwym do skalowania, co oznacza, że może być stosowana zarówno w małych laboratoriach, jak i dużych zakładach przemysłowych. Kolejną zaletą jest możliwość odzyskiwania rozpuszczalników używanych w różnych procesach technologicznych, co przyczynia się do zmniejszenia kosztów produkcji oraz ograniczenia wpływu na środowisko poprzez recykling chemikaliów.
Jakie są wyzwania związane z destylacją rozpuszczalników
Mimo licznych zalet destylacja rozpuszczalników wiąże się również z pewnymi wyzwaniami i ograniczeniami. Jednym z głównych problemów jest konieczność precyzyjnego kontrolowania warunków procesu, takich jak temperatura i ciśnienie. Niewłaściwe ustawienia mogą prowadzić do nieefektywnej separacji lub nawet degradacji cennych substancji chemicznych. Dodatkowo proces ten może być czasochłonny i wymagać znacznych nakładów energetycznych, zwłaszcza gdy chodzi o dużą skalę produkcji. Innym istotnym wyzwaniem jest konieczność stosowania odpowiednich materiałów konstrukcyjnych dla aparatury destylacyjnej, które muszą być odporne na działanie agresywnych chemikaliów oraz wysokich temperatur. W przypadku destylacji frakcyjnej pojawia się także problem związany z koniecznością posiadania skomplikowanej aparatury oraz umiejętności obsługi bardziej zaawansowanych systemów separacyjnych. Wreszcie warto zwrócić uwagę na kwestie związane z bezpieczeństwem pracy podczas przeprowadzania procesów destylacyjnych, ponieważ wiele używanych substancji chemicznych może być toksycznych lub łatwopalnych.
Jakie są zastosowania destylacji rozpuszczalników w przemyśle
Destylacja rozpuszczalników znajduje szerokie zastosowanie w różnych gałęziach przemysłu, co czyni ją jedną z kluczowych metod separacji substancji chemicznych. W przemyśle chemicznym proces ten jest wykorzystywany do produkcji czystych substancji chemicznych, takich jak kwasy, zasady czy rozpuszczalniki organiczne. Na przykład, wytwarzanie etanolu z fermentacji może być wspomagane przez destylację, co pozwala na uzyskanie wysokiej czystości alkoholu. W przemyśle petrochemicznym destylacja frakcyjna jest niezbędna do separacji różnych frakcji ropy naftowej, co umożliwia produkcję paliw, olejów i innych chemikaliów. W branży farmaceutycznej destylacja jest kluczowym procesem w produkcji leków, gdzie czystość substancji czynnych jest niezwykle ważna dla ich skuteczności i bezpieczeństwa. Dodatkowo, w laboratoriach badawczych destylacja jest często stosowana do oczyszczania reagentów oraz izolacji produktów reakcji chemicznych.
Jakie są różnice między destylacją a innymi metodami separacji
Destylacja rozpuszczalników różni się od innych metod separacji, takich jak ekstrakcja czy chromatografia, zarówno pod względem zasad działania, jak i zastosowań. Ekstrakcja polega na przenoszeniu składników z jednej fazy do drugiej na podstawie ich rozpuszczalności, co może być korzystne w przypadku mieszanin o podobnych temperaturach wrzenia. Jednakże ekstrakcja często wymaga użycia dodatkowych rozpuszczalników i może prowadzić do większych strat materiałowych. Z kolei chromatografia to technika oparta na różnicach w powinowactwie składników do fazy stacjonarnej i ruchomej, co pozwala na bardzo precyzyjne separacje, ale często wiąże się z wyższymi kosztami oraz bardziej skomplikowaną aparaturą. Destylacja natomiast jest prostsza w wykonaniu i bardziej efektywna w przypadku substancji o wyraźnie różniących się temperaturach wrzenia. Ponadto proces ten można łatwo skalować do dużych ilości, co czyni go bardziej praktycznym w przemyśle.
Jakie są nowoczesne technologie związane z destylacją rozpuszczalników
W ostatnich latach rozwój technologii związanych z destylacją rozpuszczalników znacząco wpłynął na efektywność tego procesu oraz jego zastosowania w przemyśle. Nowoczesne aparaty destylacyjne wyposażone są w zaawansowane systemy kontroli temperatury i ciśnienia, co pozwala na precyzyjne zarządzanie procesem oraz minimalizację strat materiałowych. Wprowadzenie technologii membranowych oraz systemów rekombinacyjnych umożliwia również poprawę efektywności energetycznej procesu destylacji, co jest szczególnie istotne w kontekście rosnących kosztów energii oraz dążenia do zrównoważonego rozwoju. Dodatkowo rozwijają się nowe metody destylacji, takie jak destylacja mikrofalowa czy ultradźwiękowa, które oferują szybsze i bardziej efektywne sposoby separacji składników. Te innowacje mogą znacznie zmniejszyć czas potrzebny na przeprowadzenie procesu oraz poprawić jakość otrzymywanych produktów. Również automatyzacja procesów destylacyjnych staje się coraz bardziej powszechna, co pozwala na zwiększenie wydajności produkcji oraz redukcję ryzyka błędów ludzkich podczas operacji.
Jakie są przyszłe kierunki badań nad destylacją rozpuszczalników
Przyszłość badań nad destylacją rozpuszczalników wydaje się obiecująca, zwłaszcza biorąc pod uwagę rosnące zapotrzebowanie na czyste substancje chemiczne oraz zrównoważony rozwój przemysłu. Jednym z głównych kierunków badań jest poszukiwanie nowych materiałów do budowy aparatów destylacyjnych, które będą charakteryzować się lepszą odpornością na korozję oraz wyższą efektywnością energetyczną. Badania nad nowymi technikami separacyjnymi, takimi jak hybrydowe systemy łączące różne metody (np. połączenie destylacji z ekstrakcją), mogą również przyczynić się do zwiększenia efektywności procesów separacyjnych. Inny ważny obszar to rozwój technologii odzyskiwania ciepła oraz recyklingu rozpuszczalników, co ma kluczowe znaczenie dla zmniejszenia wpływu przemysłu chemicznego na środowisko naturalne. Również badania nad zastosowaniem sztucznej inteligencji i uczenia maszynowego w optymalizacji procesów destylacyjnych mogą przynieść znaczące korzyści w zakresie wydajności i jakości produktów końcowych.
Jakie są najczęstsze błędy podczas przeprowadzania destylacji
Podczas przeprowadzania procesu destylacji rozpuszczalników istnieje wiele pułapek i błędów, które mogą prowadzić do nieefektywnych wyników lub nawet uszkodzenia sprzętu laboratoryjnego. Jednym z najczęstszych błędów jest niewłaściwe ustawienie temperatury grzania, co może prowadzić do przegrzewania cieczy lub niedostatecznego podgrzewania, skutkując niepełną separacją składników. Kolejnym problemem może być brak odpowiedniej kalibracji sprzętu pomiarowego, co wpływa na dokładność pomiarów temperatury i ciśnienia podczas procesu. Ważne jest także monitorowanie kondensatu; jego zbieranie powinno odbywać się w odpowiednich warunkach, aby uniknąć kontaminacji produktu końcowego przez niepożądane składniki. Nieodpowiednia kontrola ciśnienia może prowadzić do powstawania niebezpiecznych sytuacji, zwłaszcza gdy pracujemy z substancjami łatwopalnymi lub toksycznymi. Ponadto niedostateczna wentylacja pomieszczeń laboratoryjnych może prowadzić do nagromadzenia oparów szkodliwych dla zdrowia pracowników.
Jakie są alternatywy dla tradycyjnej destylacji rozpuszczalników
W miarę postępu technologicznego pojawiają się alternatywy dla tradycyjnej destylacji rozpuszczalników, które mogą oferować lepsze wyniki lub być bardziej przyjazne dla środowiska. Jedną z takich metod jest ekstrakcja cieczy-cieczy (LLE), która polega na oddzieleniu składników mieszaniny poprzez ich przeniesienie do innej fazy ciekłej na podstawie różnicy ich rozpuszczalności. Ta metoda może być szczególnie skuteczna w przypadku substancji o podobnych temperaturach wrzenia lub gdy konieczne jest zachowanie termolabilnych składników. Inną alternatywą jest chromatografia cieczowa wysokosprawna (HPLC), która umożliwia precyzyjne oddzielanie składników na podstawie ich interakcji z fazą stacjonarną i ruchomą. HPLC znajduje zastosowanie głównie w laboratoriach analitycznych oraz przemysłowych do analizy skomplikowanych mieszanin chemicznych. Warto również wspomnieć o technologii membranowej, która wykorzystuje półprzepuszczalne membrany do separacji składników na podstawie ich wielkości lub właściwości chemicznych.