Przemysł 4.0 to termin, który odnosi się do czwartej rewolucji przemysłowej, charakteryzującej się integracją nowoczesnych technologii w procesach produkcyjnych. W odróżnieniu od wcześniejszych rewolucji, które koncentrowały się głównie na mechanizacji i automatyzacji, przemysł 4.0 kładzie duży nacisk na cyfryzację oraz inteligentne systemy. Kluczowym elementem tego zjawiska jest Internet Rzeczy (IoT), który umożliwia urządzeniom komunikację i wymianę danych w czasie rzeczywistym. Dzięki temu przedsiębiorstwa mogą optymalizować swoje procesy produkcyjne, zwiększać efektywność oraz redukować koszty. Przemysł 4.0 zmienia także sposób, w jaki pracownicy współpracują z maszynami, wprowadzając nowe modele pracy, takie jak współpraca człowieka z robotami. Warto również zauważyć, że ta rewolucja nie dotyczy tylko dużych zakładów przemysłowych, ale także małych i średnich przedsiębiorstw, które mogą korzystać z nowoczesnych rozwiązań technologicznych, aby stać się bardziej konkurencyjnymi na rynku.
Jakie technologie są kluczowe dla przemysłu 4.0?
W kontekście przemysłu 4.0 istnieje wiele technologii, które odgrywają kluczową rolę w transformacji procesów produkcyjnych. Jedną z najważniejszych jest sztuczna inteligencja (AI), która pozwala na analizę dużych zbiorów danych oraz podejmowanie decyzji w oparciu o te analizy. AI może być wykorzystywana do przewidywania awarii maszyn, co pozwala na ich wcześniejsze serwisowanie i minimalizację przestojów. Kolejną istotną technologią jest big data, czyli analiza ogromnych ilości danych generowanych przez maszyny i urządzenia. Dzięki odpowiednim algorytmom możliwe jest wyciąganie cennych informacji, które mogą przyczynić się do poprawy efektywności produkcji. Również robotyka odgrywa kluczową rolę w przemyśle 4.0; nowoczesne roboty są coraz bardziej zaawansowane i potrafią współpracować z ludźmi w różnych zadaniach. Dodatkowo technologie takie jak chmura obliczeniowa umożliwiają przechowywanie i przetwarzanie danych w sposób elastyczny i skalowalny, co jest niezwykle ważne dla firm dążących do innowacji i szybkiego reagowania na zmiany rynkowe.
Jakie korzyści płyną z wdrożenia przemysłu 4.0?
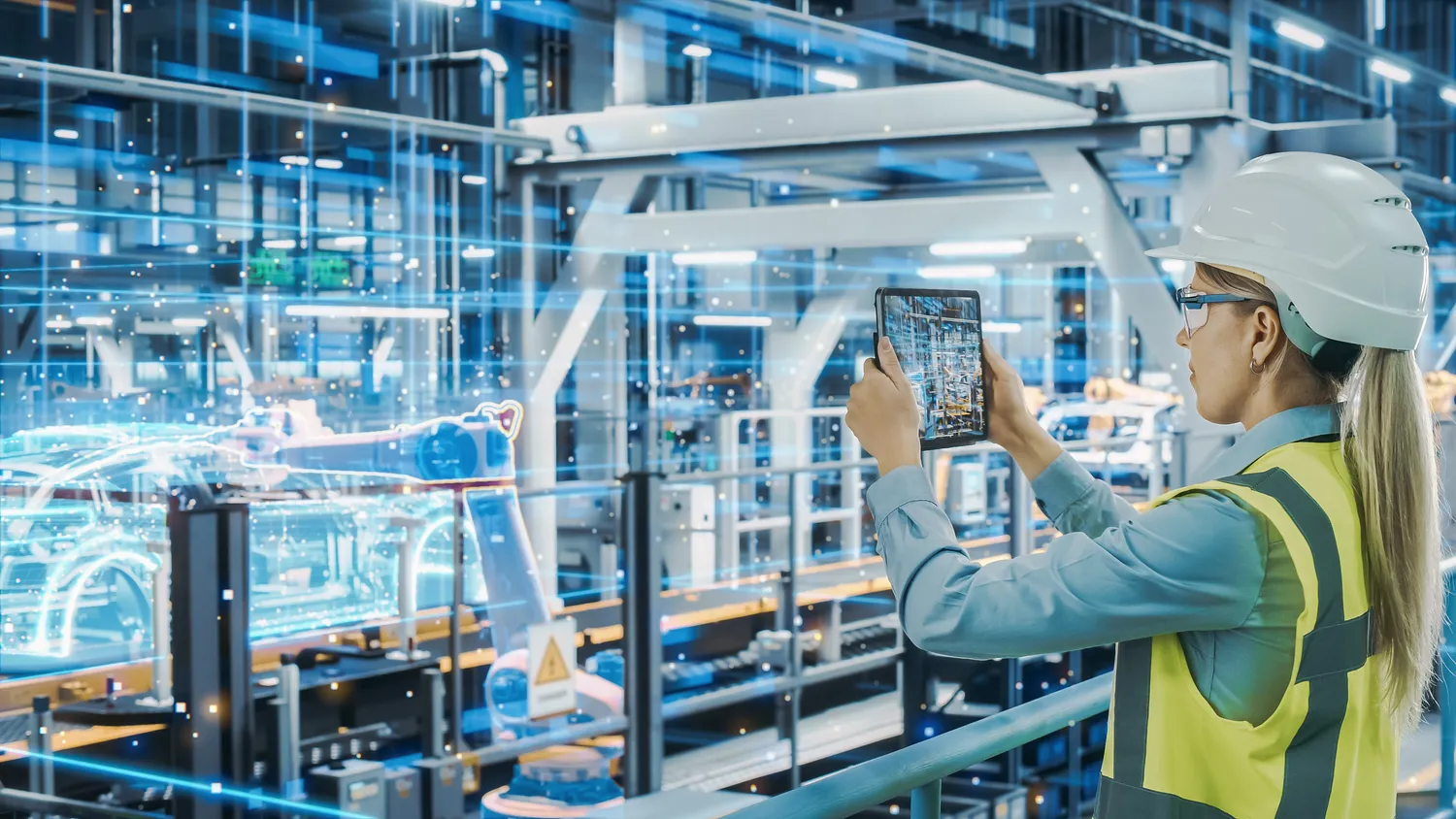
Wdrożenie zasad przemysłu 4.0 przynosi wiele korzyści zarówno dla przedsiębiorstw, jak i dla całej gospodarki. Przede wszystkim zwiększa efektywność procesów produkcyjnych poprzez automatyzację rutynowych zadań oraz optymalizację wykorzystania zasobów. Dzięki zastosowaniu nowoczesnych technologii firmy mogą lepiej zarządzać swoim czasem i kosztami produkcji, co prowadzi do większej rentowności. Kolejną korzyścią jest poprawa jakości produktów; dzięki precyzyjnym danym i analizom możliwe jest szybsze wykrywanie błędów oraz ich eliminacja na etapie produkcji. Przemysł 4.0 wpływa również na elastyczność produkcji; firmy mogą szybko dostosowywać swoje linie produkcyjne do zmieniających się potrzeb rynku oraz indywidualnych wymagań klientów. Dodatkowo integracja systemów informatycznych sprzyja lepszej komunikacji wewnętrznej oraz współpracy między działami firmy.
Jakie wyzwania stoją przed przedsiębiorstwami w kontekście przemysłu 4.0?
Mimo licznych korzyści związanych z wdrożeniem przemysłu 4.0 istnieje wiele wyzwań, które przedsiębiorstwa muszą pokonać, aby skutecznie zaimplementować nowe technologie. Jednym z największych problemów jest brak odpowiednich kompetencji wśród pracowników; wiele firm boryka się z niedoborem specjalistów znających się na nowoczesnych technologiach oraz ich zastosowaniach w praktyce. Dlatego konieczne staje się inwestowanie w szkolenia oraz rozwój umiejętności zespołów pracowniczych. Innym istotnym wyzwaniem jest integracja nowych systemów z istniejącymi rozwiązaniami; wiele przedsiębiorstw korzysta z przestarzałych technologii, które mogą być trudne do połączenia z nowoczesnymi narzędziami cyfrowymi. Ponadto kwestie bezpieczeństwa danych stają się coraz bardziej palącym problemem; wraz ze wzrostem ilości danych generowanych przez maszyny rośnie ryzyko cyberataków oraz kradzieży informacji. Firmy muszą więc inwestować w zabezpieczenia oraz strategie ochrony danych osobowych i firmowych.
Jakie są przykłady zastosowania przemysłu 4.0 w praktyce?
Przemysł 4.0 znajduje zastosowanie w różnych branżach, a jego wdrożenie przynosi wymierne korzyści. W sektorze motoryzacyjnym wiele firm korzysta z technologii IoT do monitorowania stanu pojazdów oraz optymalizacji procesów produkcyjnych. Przykładem może być wykorzystanie czujników do zbierania danych o wydajności maszyn, co pozwala na szybką reakcję w przypadku awarii. W branży spożywczej technologia blockchain zyskuje na znaczeniu; umożliwia ona śledzenie pochodzenia produktów oraz zapewnia transparentność łańcucha dostaw. Dzięki temu konsumenci mogą mieć pewność, że kupowane przez nich artykuły są świeże i pochodzą z odpowiednich źródeł. W sektorze energetycznym inteligentne sieci energetyczne (smart grids) pozwalają na efektywne zarządzanie dostawami energii oraz integrację odnawialnych źródeł energii. Firmy zajmujące się produkcją elektroniki również wdrażają rozwiązania przemysłu 4.0, takie jak automatyzacja linii montażowych czy użycie robotów współpracujących, które zwiększają precyzję i szybkość produkcji.
Jakie umiejętności są potrzebne w erze przemysłu 4.0?
W obliczu transformacji związanej z przemysłem 4.0 kluczowe staje się posiadanie odpowiednich umiejętności przez pracowników. W pierwszej kolejności istotna jest znajomość technologii cyfrowych; pracownicy powinni być biegli w obsłudze systemów informatycznych oraz narzędzi analitycznych, które umożliwiają przetwarzanie dużych zbiorów danych. Umiejętności związane z programowaniem oraz znajomość języków takich jak Python czy R stają się coraz bardziej pożądane w wielu branżach. Kolejnym ważnym aspektem jest zdolność do pracy w zespołach interdyscyplinarnych; w erze cyfryzacji współpraca między specjalistami z różnych dziedzin, takich jak inżynieria, informatyka czy zarządzanie, jest niezbędna do skutecznego wdrażania innowacji. Ponadto umiejętności analityczne oraz krytyczne myślenie stają się kluczowe dla podejmowania decyzji opartych na danych.
Jakie są przyszłe kierunki rozwoju przemysłu 4.0?
Przemysł 4.0 to dynamicznie rozwijający się obszar, który będzie ewoluował w nadchodzących latach, a jego przyszłość zapowiada się niezwykle interesująco. Jednym z kluczowych kierunków rozwoju jest dalsza integracja sztucznej inteligencji z procesami produkcyjnymi; AI będzie coraz częściej wykorzystywana do automatyzacji skomplikowanych zadań oraz podejmowania decyzji na podstawie analizy danych w czasie rzeczywistym. Również rozwój technologii 5G wpłynie na przemysł 4.0; dzięki szybszym prędkościom przesyłu danych możliwe będzie jeszcze bardziej zaawansowane wykorzystanie IoT oraz komunikacji między urządzeniami. W kontekście zrównoważonego rozwoju coraz większy nacisk kładzie się na ekologiczne aspekty produkcji; technologie umożliwiające recykling materiałów oraz zmniejszenie zużycia energii będą miały kluczowe znaczenie dla przyszłości przemysłu. Dodatkowo rozwój autonomicznych systemów produkcyjnych, które będą mogły działać bez ludzkiej interwencji, stanie się realnością w wielu branżach.
Jakie są różnice między przemysłem 4.0 a wcześniejszymi rewolucjami przemysłowymi?
Przemysł 4.0 różni się od wcześniejszych rewolucji przemysłowych pod wieloma względami, co czyni go unikalnym zjawiskiem w historii gospodarki. Pierwsza rewolucja przemysłowa koncentrowała się głównie na mechanizacji produkcji za pomocą maszyn parowych, co znacznie zwiększyło wydajność pracy ludzkiej. Druga rewolucja przyniosła elektryczność i masową produkcję, co pozwoliło na tworzenie produktów na dużą skalę przy użyciu taśm montażowych. Trzecia rewolucja to era automatyzacji i komputerów, która umożliwiła bardziej precyzyjne sterowanie procesami produkcyjnymi dzięki zastosowaniu technologii informacyjnych. Przemysł 4.0 natomiast skupia się na cyfryzacji i integracji różnych technologii, takich jak IoT, AI czy big data, co prowadzi do powstania inteligentnych fabryk zdolnych do samodzielnego podejmowania decyzji i optymalizacji procesów w czasie rzeczywistym.
Jakie są kluczowe elementy strategii wdrożenia przemysłu 4.0?
Aby skutecznie wdrożyć zasady przemysłu 4.0, przedsiębiorstwa muszą opracować kompleksową strategię obejmującą kilka kluczowych elementów. Po pierwsze, konieczne jest przeprowadzenie analizy obecnego stanu technologicznego firmy oraz identyfikacja obszarów wymagających modernizacji lub optymalizacji. Następnie warto określić cele wdrożenia technologii 4.0; mogą one obejmować zwiększenie efektywności produkcji, poprawę jakości produktów czy redukcję kosztów operacyjnych. Kolejnym krokiem jest inwestycja w odpowiednie technologie oraz szkolenie pracowników; bez dobrze przeszkolonego zespołu nawet najnowocześniejsze rozwiązania nie przyniosą oczekiwanych rezultatów. Ważne jest także stworzenie kultury innowacji w organizacji; pracownicy powinni być zachęcani do dzielenia się pomysłami i proponowania ulepszeń procesów pracy.
Jakie są najczęstsze błędy przy wdrażaniu przemysłu 4.0?
Wdrożenie przemysłu 4.0 wiąże się z wieloma wyzwaniami, a przedsiębiorstwa często popełniają błędy, które mogą negatywnie wpłynąć na efektywność całego procesu. Jednym z najczęstszych błędów jest brak odpowiedniego planowania; wiele firm przystępuje do wdrożenia nowych technologii bez dokładnej analizy swoich potrzeb oraz możliwości. Kolejnym problemem jest niewłaściwe zarządzanie zmianą; pracownicy mogą być oporni na nowe rozwiązania, jeśli nie zostaną odpowiednio przeszkoleni i zaangażowani w proces transformacji. Również niedostateczne inwestycje w infrastrukturę technologiczną mogą prowadzić do nieefektywnego wykorzystania nowoczesnych narzędzi. Warto również zwrócić uwagę na kwestie związane z bezpieczeństwem danych; wiele firm zaniedbuje zabezpieczenia, co naraża je na ryzyko cyberataków. Ostatecznie brak ciągłego monitorowania postępów oraz elastyczności w dostosowywaniu strategii do zmieniających się warunków rynkowych może skutkować nieosiągnięciem zamierzonych celów.